Numerical and experimental study of fatigue crack growth in autofrettaged two-layer cylindrical pressure vessel - دانشکده فنی و مهندسی
Numerical and experimental study of fatigue crack growth in autofrettaged two-layer cylindrical pressure vessel
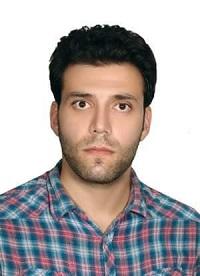
نوع: Type: thesis
مقطع: Segment: PHD
عنوان: Title: Numerical and experimental study of fatigue crack growth in autofrettaged two-layer cylindrical pressure vessel
ارائه دهنده: Provider: Mohamad Sajad Khodayari
اساتید راهنما: Supervisors: Rahman Seifi
اساتید مشاور: Advisory Professors: دکتر رحمن سیفی ( استاد تمام)
اساتید ممتحن یا داور: Examining professors or referees: Amir Hossein Mahmoudi, Ali Pour Kamali Anaraki, Ali Shahrjerdi
زمان و تاریخ ارائه: Time and date of presentation: 2024
مکان ارائه: Place of presentation: Conference Room
چکیده: Abstract: Numerical and experimental study of fatigue crack growth in autofrettaged two-layer cylindrical pressure vessel Abstract: The processes of autofrettage and interference in multi-layer cylinders are among the conventional methods of creating compressive residual stresses in the walls of thick-walled vessels. To achieve the higher strength and fatigue life, the combination of these processes was also used. J-Integral is one of the major parameters based on energy in the fracture mechanics, which is used to predict the crack propagation in elastoplastic strain fields. In this study, by using numerical and experimental methods, the propagation of a semi-elliptical crack on the inner surface of a autofrettaged and interferenced two-layered cylindrical vessel subjected to pulsating internal pressure, was investigated. The fatigue life and bursting pressure of this vessel have been calculated based on the critical J-integral criterion. Then, the effects of the various parameters such as the depth, shape and angle of the crack, autofrettage ratio of the inner and outer layers, radial interference and the ratio of the thickness of the layers on the fatigue life and bursting pressure was investigated. The material of the inner and outer layers is AL-7075 T6. The non-linear hardening behavior of this alloy has predicted using the Chaboche's model. The validity of the numerical results has been checked and acceptable accuracy of the numerical results proved by experimental data. Combination of two processes of the autofrettage and radial interference in double-layer cylinders causes the fatigue life and burst pressure of two-layer cylindrical vessel to increase several times. So that the fatigue life of the studied vessel with an axial crack is about 10 times that of a single-layer vessel with the same axial crack. Also, bursting pressure of the interference and autofrettaged double-layer vessel with internal cracks was higher than the single-layer vessel without cracks with the same dimensions. The increase of crack orientation angle and crack aspect ratio have caused an increase of the fatigue life and burst pressure. The decrease of interference from 0.1 to 0.05 mm has caused a decrease of 0- 13% in the burst pressure and 0- 93% in the fatigue life of two-layer cylinder with axial crack, while, there is no effects for a circumferential crack. The fatigue life and bursting pressure increases with the increase of the autofrettage percent of the inner layer. The autofrettage percent of the outer layer has no considerable effects on the life and burst pressure. Keywords: Autofrettage, Interference, Fatigue life, Bursting pressure, Crack growth
فایل: ّFile: Download فایل